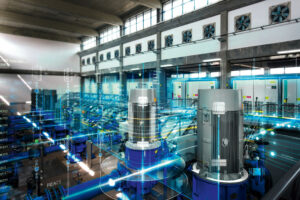
Bild 1: Ab 1.7.2021 müssen Elektromotoren flächendeckend der Effizienzklasse IE3 oder höher entsprechen; Quelle: Siemens
Seit 2009 gelten die europäischen Ökodesign-Vorschriften für Elektromotoren. Mit Wirkung zum 1.7.2021 ersetzt eine weitere Neuauflage die bisherigen Regelungen. Damit kommen auf Anlagenbetreiber neue Anforderungen zu, denn entsprechende Motoren müssen nun flächendeckend der Effizienzklasse IE3 oder höher entsprechen.
In der EU sind etwa 8 Mrd. Elektromotoren im Einsatz, die fast 50 % des in der EU erzeugten Stroms verbrauchen (Quelle: Europäische Kommission, https://ec.europa.eu). Den größten Anteil machen dabei industriell genutzte Drehstrom-Asynchronmotoren aus, kurz Drehstrommotoren: Auf sie entfallen geschätzt rund 80 % aller weltweit durch Elektromotoren verbrauchten Energie (Bild 1).
Vor diesem Hintergrund hat die EU im Jahr 2009 die Ökodesign-Verordnung (EG) Nr. 640/2009 für Elektromotoren auf den Weg gebracht. Das Energieeffizienzniveau wird darin in internationalen Energieeffizienzklassen (IE) angegeben, wobei IE1 die niedrigste und IE4 die höchste Klasse beschreibt. Die Energieeffizienz eines Elektromotors berechnet sich dabei als das Verhältnis der mechanischen Ausgangsleistung zur elektrischen Eingangsleistung.
Gemäß der seit 2017 geltenden Fassung der Ökodesign-Verordnung müssen alle Drehstrommotoren mit einer Ausgangsleistung zwischen 0,75 kW und 375 kW die Energieeffizienzklasse IE3 erfüllen. Lediglich die Kombination von IE2-Motoren mit Frequenzumrichtern sowie sehr kleine und sehr große Leistungen waren zusammen mit einigen Sonderbauformen bisher noch ausgenommen. Diese Lücken werden nun geschlossen.
Neue Ökodesign-Anforderungen ab Juli 2021
Mit Wirkung vom Juli 2021 werden die bisherigen Regelungen durch die Verordnung (EU) 2019/1781 zur Festlegung von Ökodesign-Anforderungen an Elektromotoren und Drehzahlregelungen ersetzt (Tabelle 1). Die neuen Vorschriften gelten auch für mehrere bisher nicht erfasste Drehstrommotoren, wie insbesondere
- kleinere Motoren mit einer Leistung zwischen 120 W und 750 W,
- größere Motoren mit einer Leistung zwischen 375 kW und 1 MW sowie
- 60-Hz-Motoren, achtpolige Motoren und Einphasenmotoren (letztere erst ab Juli 2023).
Darüber hinaus wird das Anforderungsniveau steigen: Dreiphasenmotoren mit einer Nennausgangsleistung zwischen 0,75 kW und maximal 1 MW müssen bis Juli 2021 das Effizienzniveau der Klasse IE3 erreichen. Für Motoren mit einer Leistung zwischen 75 kW und 200 kW ist ab Juli 2023 sogar das Effizienzniveau der höchsten Klasse IE4 gefordert.
Die Verordnung enthält außerdem Vorschriften für die Effizienz von Drehzahlregelungen. Für diese gelten, ebenso wie für Motoren, Informationsanforderungen, etwa in Bezug auf die Effizienz bei unterschiedlichen, durch Drehzahl und Drehmoment definierten Betriebspunkten. Dies wird Anwendern dabei helfen, die Effizienz ganzer Systeme zu optimieren.
Wie bereits in der vorherigen Verordnung sind einige, für bestimmte Bedingungen ausgelegte Motoren von den Anforderungen ausgenommen, so zum Beispiel Motoren, die in einer Flüssigkeit arbeiten (beispielsweise in Abwassersystemen).
Konsequenzen für Anlagenbetreiber
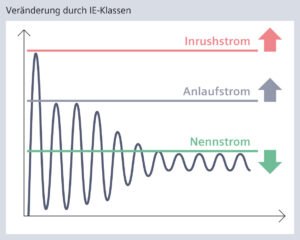
Bild 2: Der bei Effizienzmotoren deutlich höhere Einschaltstrom kann bisher eingesetzte Schalt- und Schutzgeräte überfordern und beim Start zu Fehlauslösungen führen; Quelle: Siemens
Zusammengefasst müssen künftig also Drehstrommotoren im Bereich von 750 W bis 1 MW der Effizienzklasse IE3 oder höher entsprechen. Für den Anwender bedeutet das: Er muss sich unter Umständen auf andere Bauformen einstellen und sowohl mit elektrischen als auch mechanischen Anpassungen rechnen. Daher bietet es sich an, den kompletten Antriebsstrang zu betrachten: Denn nicht immer passt die Leistung des Motors zur Applikation. Vielmehr sind Motoren aus planerischer Vorsicht oft überdimensioniert und werden in der Praxis in der geplanten Größe gar nicht gebraucht. Auch eine elektronische Drehzahlanpassung wird keineswegs immer benötigt. Und viele Motoren lassen sich mit Nenndrehzahl effizienter betreiben. Gerade bei Serienmaschinen bedeutet das finanzielle Einsparpotenziale.
Aber auch Betreiber entsprechender Anlagen sind betroffen, da sie bei einer Modernisierung oder im Fehlerfall nur noch die modernen Effizienzmotoren als Ersatz angeboten bekommen. Mit einem Austausch des Motors allein ist es dann aber nicht getan. Denn der bei Effizienzmotoren deutlich höhere Einschaltstrom kann bisher eingesetzte Schalt- und Schutzgeräte überfordern und beim Start zu Fehlauslösungen führen (Bild 2). Als Alternativen bieten sich Motor- und Sanftstarter an. Die Produktfamilie »Sirius« von Siemens zum Beispiel ist komplett »IE3/4-ready« (Bild 3).
Motorstarter für mehr Energieeffizienz
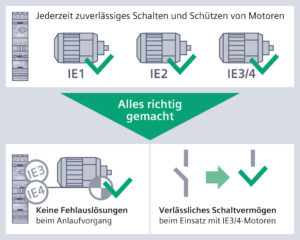
Bild 3: Motor- und Sanftstarter wie »Sirius« erfüllen die Anforderungen IE3 und IE4; Quelle: Siemens
Die Frage, welche Art von Motorstarter die jeweils sinnvollste ist, hängt immer von der Anwendung ab. Sofern der Betrieb bei Nenndrehzahl dem Bedarf der Applikation entspricht und das relativ hohe Anlaufmoment kein mechanisches Problem erzeugt, ist ein elektromechanisch geschaltetes Schütz oder ein kompakter Motorstarter in Relaisbauweise die wirtschaftlichste Lösung. Für viele Standardanwendungen ist dies nach wie vor das Maß der Dinge.
Anders bei Anwendungen mit zum Beispiel größerer Massenträgheit: Um dabei Fehlfunktionen auszuschließen, werden bei Festdrehzahlbetrieb inzwischen häufig Sanftstarter verwendet – eine kompakte und kostengünstige Antriebslösung. Sie bieten dank vielfältiger, parametrierbarer Funktionen weit mehr Möglichkeiten für eine Anpassung an die jeweilige Applikation. Zudem wirken sie strombegrenzend im Anlauf, was gerade bei großen Lasten vom Netzbetreiber gefordert sein kann. Durch eine sogenannte Bypass-Schaltung nach dem Hochlauf erzeugen sie zudem nur geringe Abwärme im Schaltschrank, was eine Zwangsbelüftung oder Klimageräte überflüssig machen kann. Sanftstarter gelten daher nicht zuletzt aus Effizienzgründen als erste Wahl.
Weil bei wechselnden Lasten oder unterschiedlichen Geschwindigkeiten Festdrehzahlantriebe überfordert sind, kommen in diesen Fällen Frequenzumrichter zum Einsatz. Mittels moderner Leistungselektronik ermöglichen sie es, die Drehzahl an die jeweilige Last flexibel anzupassen und bei Bedarf auf dem geforderten Punkt zu halten. In manchen Ausführungen besteht zudem die Notwendigkeit, geregelt zu bremsen. Die dadurch entstehende Energie können funktionell hochwertigere Frequenzumrichter ins Netz zurückspeisen.
Steigende Energieeinsparungen
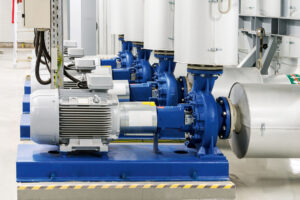
Bild 4: Die aktuell geltende Verordnung für Motoren spart bisher pro Jahr 57 TWh elektrische Energie ein; Quelle: Siemens
Nicht zuletzt durch die bisherigen und künftigen europäischen Ökodesign-Vorschriften kann der Einsatz eines effizienteren Motors, je nach Leistung und Verwendung, über seine Lebensdauer Einsparungen von einigen wenigen bis hin zu mehreren 10.000 € bewirken (Bild 4). Im Rahmen der bisher geltenden Verordnung führte die Verwendung effizienterer Motoren zuletzt zu Energieeinsparungen in Höhe von 57 TWh im Jahr.
Unter Berücksichtigung der Gesamtwirkung der überarbeiteten Verordnung werden voraussichtlich die jährlichen Einsparungen bis 2030 auf 110 TWh ansteigen, was dem Stromverbrauch der Niederlande entspricht. Dies bedeutet, dass jährlich 40 Mio. t CO2-Emissionen vermieden und die jährlichen Energiekosten in der EU bis 2030 um rund 20 Mrd. € sinken werden (Quelle: Europäische Kommission, https://ec.europa.eu).
Autor
Andreas Thomas, Marketing Manager Electrical Products, Siemens Smart Infrastructure
Quelle und Bildquelle: www.elektro.net